Transforming Agriculture Operations for Efficiency
Reducing inventory waste by 30% and enhancing cross-functional collaboration.
Role
Product designer
Project type
Product design
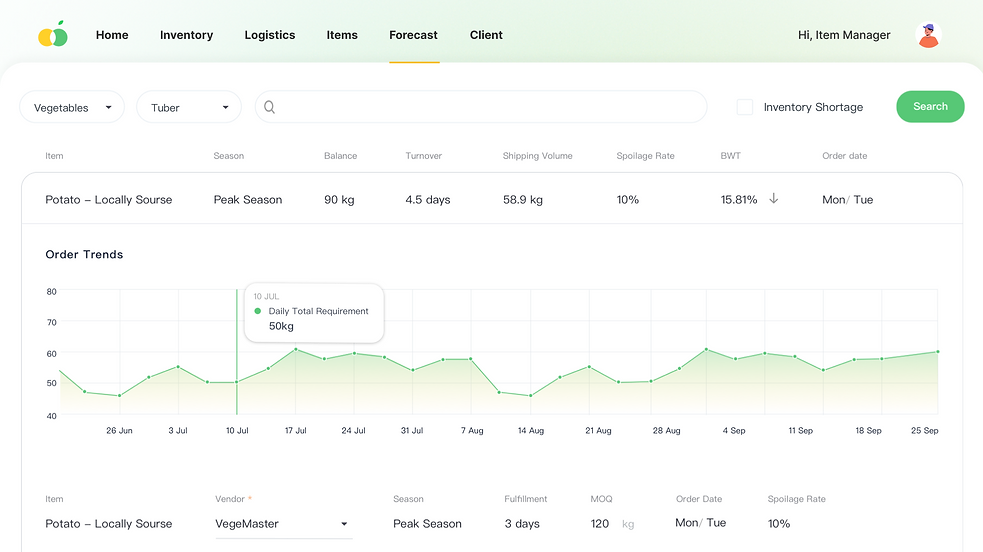
Understanding user needs
Insights from cross-team
After intervening with cross-functional teams- including supply, operations, finance, and client teams- I uncovered critical inefficiencies impacting the company's ability to scale effectively and identified opportunities to address these challenges.
1
Inconsistent Supply
Pain point
The company struggles to supply common items reliably, forcing clients to seek alternatives.
Opportunity
Creating a centralized system to ensure stable product availability and better inventory planning.
2
Lack of Stock Visibility
Pain point
Inventory waste was caused by multiple uncoordinated factors, including poor stock rotation, unpredictable spoilage, and inefficient procurement cycles.
Opportunity
A transparent inventory tracking system would help teams make data-driven decisions on stock rotation, expiration management, and restocking priorities.
3
Procurement Misalighment
Pain point
Supply and operation teams made procurement decisions independently, without real-time data on each other's actions.
Opportunity
A synchronized procurement system that connects both teams in real time would reduce overstocking, prevent redundant purchases, and optimize supply planning.
Defining the System: A Data-Driven Roadmap
Based on insights from cross-functional research, I structured a master data framework to capture all essential data points across supply, operations, client managment, and procurement workflows.
This roadmap serves as the system's backbone, aligning teams into a cohesive, scalable structure that ensures real-time, accurate data informs every decision.
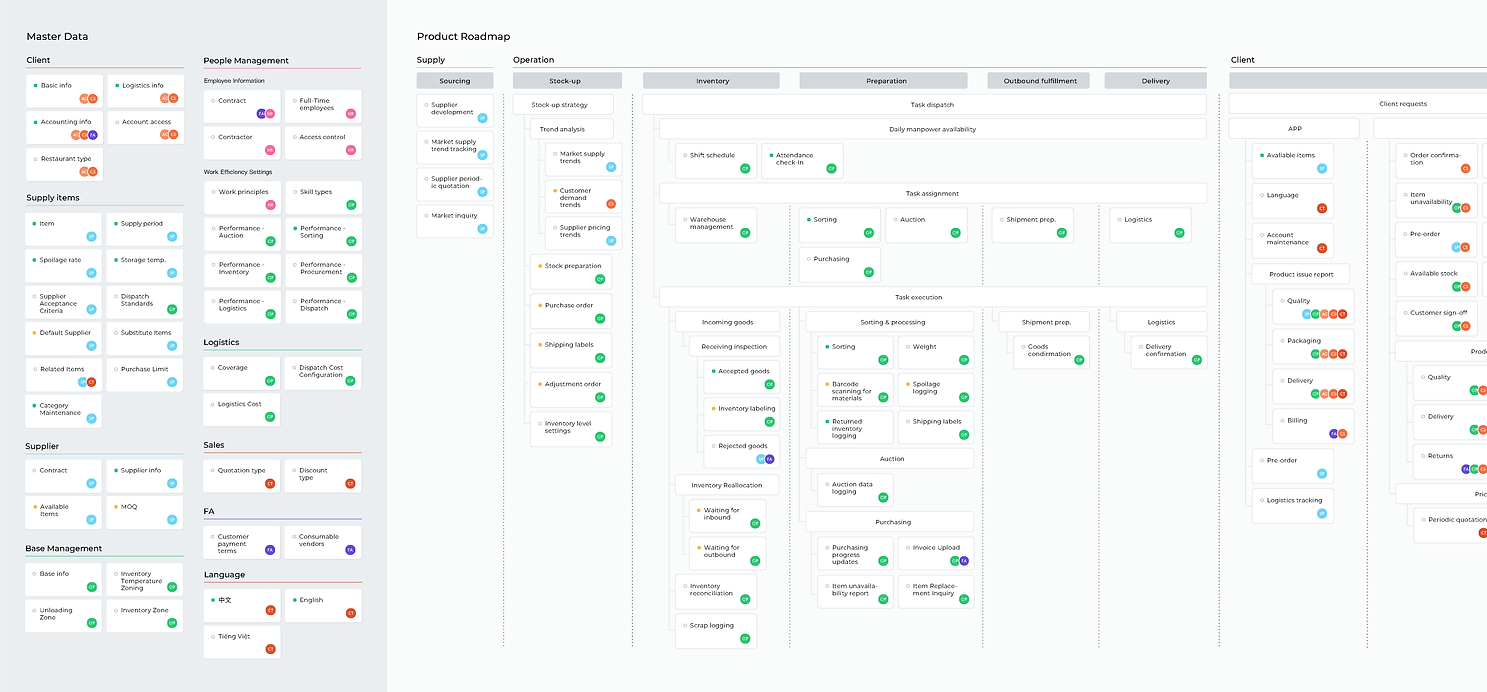
Ideate & Prototype
Designing for transparency & efficiency
With the master data framework in place, I translated strategic insights into functional solutions that improve inventory transparency, procurement efficiency, and supply coordination. The following interfaces demonstrate how the system streamlines key workfloes and eliminates communication gaps across teams.
Item Management System
Solving inconsistent supply
Impact
-
Standardized product and supplier data, ensuring procurement consistency.
-
Reduced last-minute sourcing issues by improving inventory visibility.
-
Enabled a shared data source, aligning procurement and inventory teams.

Stock Fulfillment Decision-Making Tool
Optimizing procurement with smarter vendor selection
Impact
-
Prioritized vendor selection optimizes procurement based on quality, cost, and delivery efficiency.
-
Minimized spoilage and waste by aligning vendor choises with historical performance and demand forcasting.
-
Reduce stock-up by selecting cost-efficient suppliers while maintaining quality standars.
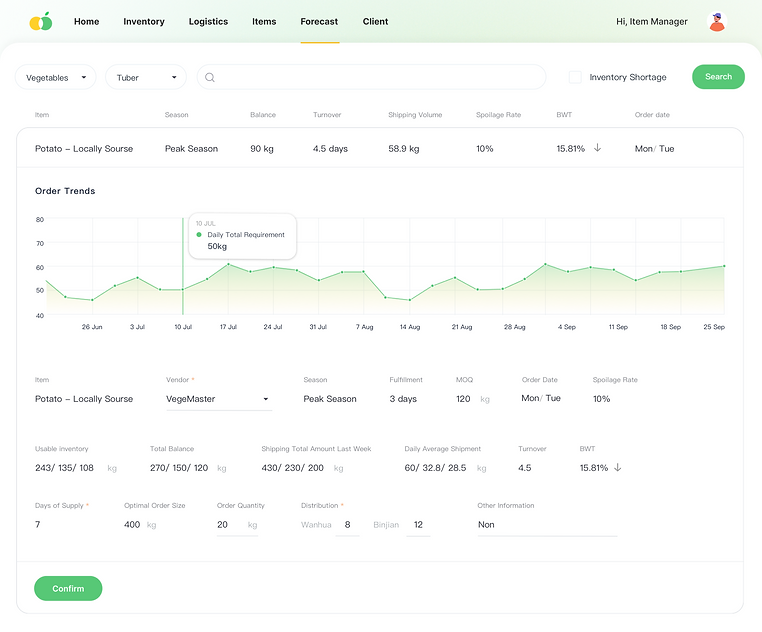